MISSION
What drives us at Will-Fill
Will-Fill equips metalworking machines with a unique add-on that relieves operator workload and reduces the ecological footprint of production. The fully automatic control unit monitors coolant quality. The optimum fluid level is maintained by automated filling processes linked to electronic measurements set according to each specific need. When the quality of the metalworking fluid changes, Will-Fill can adjust it or send a notification when action is needed.
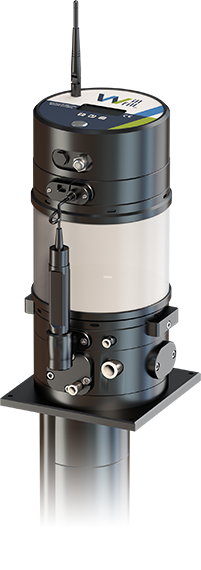
History
Will-Fill is developed, produced and marketed by DIERICKX Tools, a small Belgian mechanical engineering family firm. Since 2020 Will-Fill is a stand-alone business unit of DIERICKX Tools. This shortens the communication lines between R&D, production and the market, and allows us to respond much faster to customer questions.
We developed Will-Fill because we needed it!
In many precision engineering and mechanical workshops like ours, the focus is on the production process and machine output. Emulsion management is not a priority because taking care of the emulsion requires repetitive actions that can be easily forgotten.
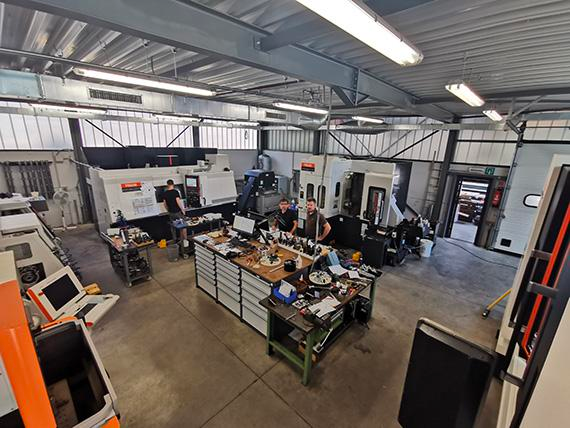
JOBS
Will-Fill was developed by a team of engineers-entrepreneurs, with each team member carrying great responsibility within his or her domain. Are you eager to learn, able to persevere and want to make a difference?
Apply on-spec: jobs@will-fill.com
Industry 4.0
Smart factories, some even speak of a fourth industrial revolution. In the factories of the future, routine tasks will be taken over by smart automation, so that the creative (and the most pleasant!) tasks can be fully carried out by people. How is Will-Fill contributing to this? The device was developed to handle four routines: filling, measuring, reporting and conditioning. Thus Will-Fill takes over these repetitive tasks from an organisation’s employees
M2M
At Will-Fill, the story does not stop at the factory gate. Because Will-Fill is equipped with machine-to-machine technology, the service can be brought to a higher level. Information from recurring status checks and necessary interventions make possible the generation of measurement reports that are easily accessible to the customer or other relevant party. This then translates into firmware updates that make the measurements even better and offer the customer more functions.